KetaSpire PEEK XT-920 eleva significativamente el límite superior de temperatura del PEEK tradicional, abriendo nuevas aplicaciones en componentes moldeados por inyección y mecanizados para esta familia de polímeros de ultra alto rendimiento.
Con la misma proporción 2:1 de éter (E) y cetona (K), el PEEK XT de alta temperatura presenta la misma resistencia química excepcional que el PEEK tradicional. Esta estructura polimérica también ofrece resistencia a una gama más amplia de sustancias químicas, en comparación con policetonas como PEK, PEKK, PEKEKK y PAEK, que tienen relaciones éter-cetona algo diferentes.
Aunque su resistencia química es comparable a la del PEEK, la química exclusiva que condujo al desarrollo del PEEK XT eleva su temperatura de transición vítrea a 170 °C (338 °F), es decir, 20 °C (36 °F) más que los grados anteriores de PEEK, incluidos el KetaSpire KT820 NT y el Victrex 450G.
Los componentes moldeados por inyección o mecanizados con KetaSpire PEEK XT también conservan su resistencia a temperaturas extremas. Según los datos de propiedades de Solvay, que produce los polímeros KetaSpire PEEK, el grado XT tiene un módulo de tracción un 400% mayor y aproximadamente un 50% más de resistencia a la tracción a 160°C (320°F) que el PEEK tradicional. También ofrece una resistencia dieléctrica y una resistividad volumétrica mejoradas, lo que lo convierte en un candidato sólido para aplicaciones eléctricas a alta temperatura.
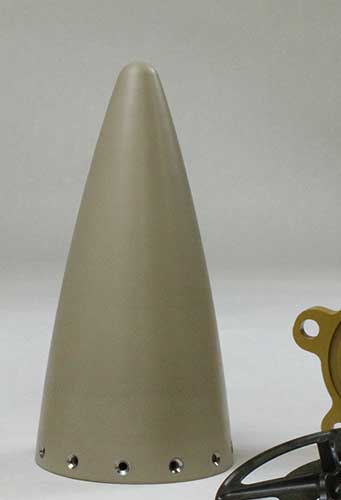
Clases de PEEK XT para componentes moldeados por inyección
Solvay ofrece KetaSpire PEEK en tres grados: PEEK XT-920 sin reforzar, y KetaSpire XT-920 CF30 reforzado con un 30% de fibra de carbono y KetaSpire XT-920 GF30 reforzado con un 30% de fibra de vidrio. Las fórmulas reforzadas con fibra proporcionan más resistencia estructural para aplicaciones que deben soportar cargas y presiones elevadas.
Tecnología de moldeo por inyección de polímeros PEEK XT reforzados y sin relleno
Los clientes reconocen la experiencia de Drake Plastics en el desarrollo de utillaje, condiciones de proceso y configuraciones de equipos para polímeros avanzados que producen piezas moldeadas por inyección con tolerancias de precisión, tensión mínima y rendimiento óptimo. El XT920 se procesa a temperaturas mucho más altas que el PEEK, y su ventana de procesamiento es más estrecha. El diseño y el control precisos del proceso son factores clave para conseguir las propiedades de alto nivel de los grados de PEEK KetaSpire XT, y más aún para las formulaciones reforzadas con un 30% de fibra de vidrio o de carbono.
El análisis del flujo de fusión como hoja de ruta:
El laboratorio de Drake Plastics dispone de las herramientas analíticas para determinar las características de flujo de fusión de los polímeros como guía para los mejores parámetros de procesamiento y diseño de herramientas para cada grado de PEEK XT.
Nuestros técnicos de utillaje utilizan la información para el diseño de las compuertas, a fin de conseguir una orientación de las fibras que optimice la resistencia de los componentes moldeados. Los datos analíticos también definen las condiciones del proceso que preservarán las propiedades inherentes de cada grado de PEEK XT.
La tecnología de moldeo optimiza el rendimiento y la calidad:
Drake Plastics utiliza máquinas de moldeo totalmente eléctricas que funcionan de forma constante y eficaz, y eliminan el riesgo de fugas o derrames hidráulicos.
Nuestros ingenieros dimensionan los barriles a cada polímero, para minimizar el tiempo a temperatura durante el moldeo. Esto evita la degradación del polímero en la fase fundida y garantiza las máximas propiedades y consistencia de cada pieza moldeada.
La inversión de Drake Plastics en los sistemas de control RJG contribuye aún más a la calidad y el rendimiento constantes de los componentes moldeados por inyección de PEEK XT-920. El equipo supervisa las condiciones en la cavidad del molde y mantiene las temperaturas y presiones de proceso ideales para cada grado de PEEK XT-920.
Las aplicaciones de PEEK XT de alta temperatura incluyen componentes grandes con espesores de pared elevados que pueden sufrir hundimientos superficiales o vacíos internos al moldearlos. Las máquinas de moldeo por inyección de Drake Plastic están equipadas con capacidades de compresión que permiten consolidar piezas de paredes pesadas durante el ciclo de enfriamiento. Esta secuencia de postinyección comprime o «acuña» la pieza dentro del molde para obtener piezas de paredes gruesas sin huecos ni porosidades.
Gama de tamaños versátil:
Los tamaños de máquina entre 35 y 300 toneladas proporcionan a los clientes una gama de componentes moldeados por inyección de 0,85 gramos (0,03 oz.) a 567 gramos (20 oz.). Esta capacidad sirve para toda la gama de aplicaciones de equipos de la industria del petróleo y el gas, desde componentes eléctricos de precisión hasta grandes válvulas y juntas.
Aplicaciones de PEEK XT de alta temperatura KetaSpire
Los tres grados de KetaSpire XT-920 son ideales para componentes expuestos a temperaturas superiores a la Tg de los grados tradicionales de PEEK, donde pierden rápidamente resistencia y rigidez, y su índice de expansión térmica aumenta drásticamente. Las propiedades de aislamiento eléctrico también disminuyen drásticamente a temperaturas superiores a la Tg del polímero.
Las pruebas con gas ácido NORSOK M710 demostraron las capacidades del polímero para aplicaciones en entornos de fondo de pozo. Tras 50 días de exposición a un 20% de H2Sa 230°C y 14 días de exposición a salmuera/HC a 300°C, el PEEK XT se comportó de forma comparable al PEEK tradicional, un material reconocido mundialmente por su fiabilidad en componentes de equipos de petróleo y gas.
Entre las aplicaciones típicas que pueden utilizar PEEK XT como mejora del PEEK tradicional para temperaturas más elevadas se incluyen los asientos de válvulas, juntas y anillos de junta de apoyo, conectores eléctricos en ESP, bobinas, espirales y radomos.
Prototipos y Componentes Mecanizados a partir de Formas de Stock de PEEK XT de KetaSpire
Drake Plastics extrude todos los grados de KetaSpire PEEK XT-920 en barras y placas mecanizables en stock y en tamaños personalizados. Nuestra operación de mecanizado CNC convierte rutinariamente estas formas en prototipos para probar y validar el diseño y el rendimiento de los componentes antes de invertir en herramientas de moldeo por inyección. También ayudamos a los clientes con cantidades de producción de piezas mecanizadas en caso de que se necesiten antes de finalizar el utillaje de producción.
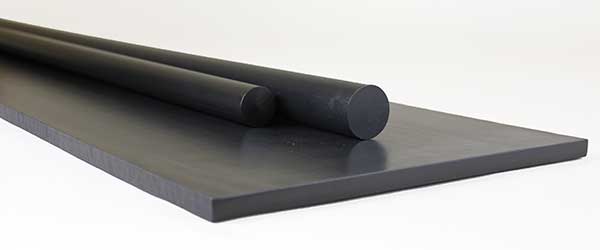